Revolutionizing the Pharmaceutical Industry

In the intricate world of pharmaceuticals, precision, hygiene, and efficiency are paramount. Enter the filling and capping machines and monoblocks – the unsung heroes of the industry. These state-of-the-art machines play a pivotal role in ensuring that medications are packaged securely and accurately, safeguarding the health of millions worldwide. This article delves into the mechanics and innovations behind these machines, highlighting their significance in upholding the stringent standards of the pharmaceutical sector. From liquid formulations to powders, and from vials to capsules, discover how these technological marvels are shaping the future of medicine production and distribution.
Filling and Capping Monoblocks for Liquid Products
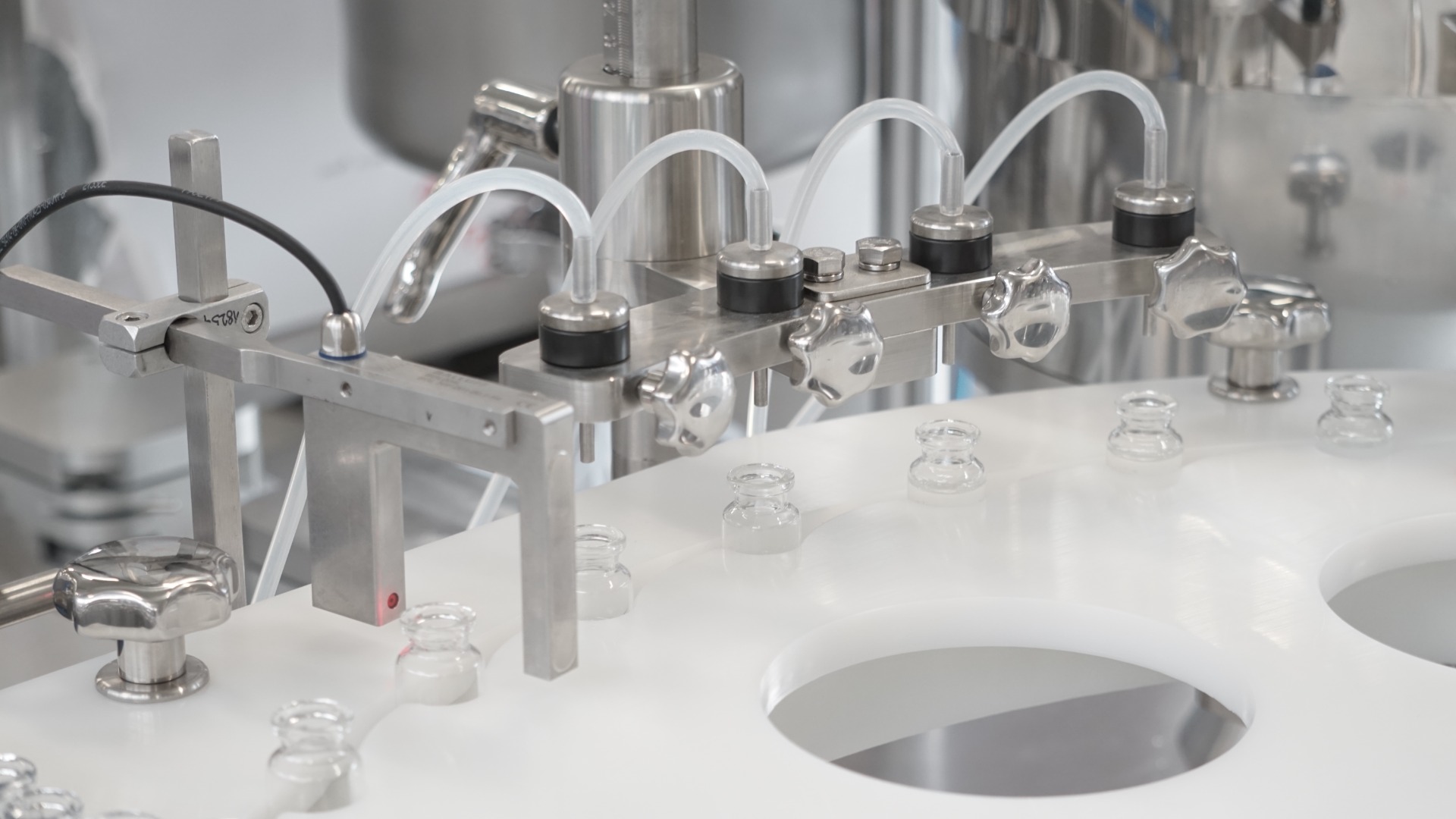
Key Features:
Stainless steel machine frame with adjustable height legs.
Motorized conveyor with adjustable speed.
Starwheel for container transfer between stations.
Product tank with product level control.
Filling station equipped with peristaltic pumps or flowmeters.
Vibrating or rotary caps orientator.
Capping head with adjustable torque.
Control panel featuring a touch screen.
CE safety guards.
Overview:
Empty vials or other containers are transported by the infeed conveyor to the starwheel. A sensor detects the presence of vials at the entrance. The first station is for filling, and the machine can have 1 to 6 filling positions. Various dosing systems are available, including peristaltic pumps, lobe pumps, and flowmeters. After filling, the next operation is capping. The standard machine comes with a capping device for screw caps, which includes a caps feeder, chute, pick and place device, and capping head. This device can be replaced with other systems like crimping. Additional capping units for droppers, dosers, or rubber stoppers can be added. Once filled and closed, the containers exit the machine on the outfeed conveyor.
Robotic Filling and Sealing of metal and plastic tubes
Key Features:
Working height according the tube length setting centrally by motorisedlifting
Servo driven indexing oval table with tube holders-speed adjustable onHMI
Photocell tube orientation system with servo control
Motorised volumetric filling system - volume and parameters adjustable onHMI
Motorised lifting and closing filling nozzle (up and bottom filling oftube)
Hot air tube heating unit with air blowing pump
Linear cam mechanically driven sealing jaws with marking to the weld
Linear cam mechanically driven trimming unit
Ejection unit unit and slide outfeed
Available for sealing of metallic tubes also (with optional changeoverkit)
Overview:
The TUBELINE P 6000 Duplex is an automatichigh speed machine is designed to fill and close plastic and laminate tubes byhot air welding. Machine can be used for filling of liquid products. Machine is duplex, it means each step handles2 tubes a time to speed up whole process. Tube is loaded automatically from thebox using a robot with sophisticated grippes.
Tubes are handled in the nests and itsmovement is done by special oval type carousel which allows fast transferringinto each position.
Closing jaws are equipped with exchangeableset of marks, date and batch in a weld.The machine is designed especially for food, pharma and cosmetic industry.
Filling is done by volumetric pumps with changeableranges of volumes (up to 300ml v). Also nozzle tips must be changed accordingthe tube size. Nozzle tip is a changeable bottom part of nozzle includingclosing of nozzle and blowing of the product "hair".
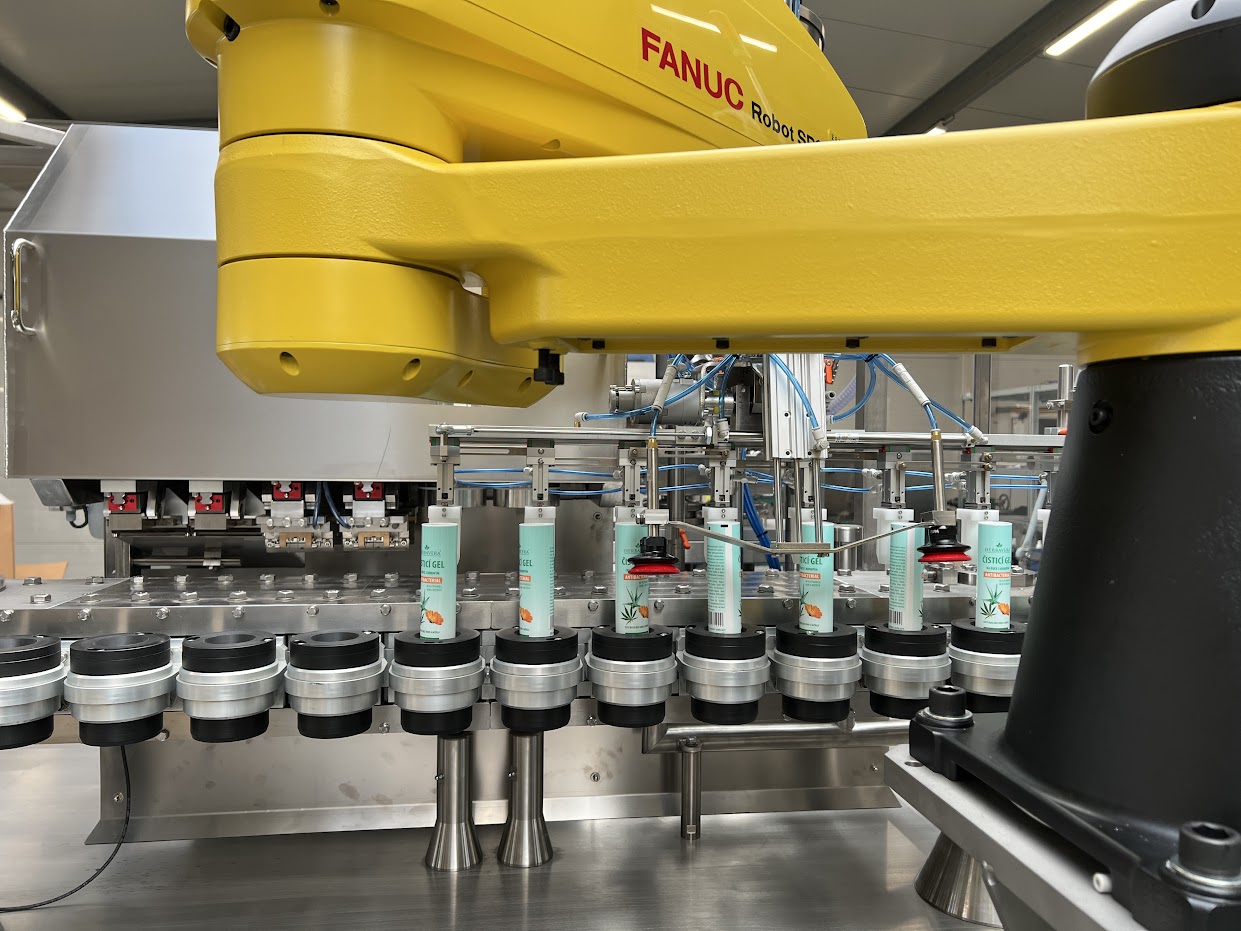
Machines for Filling and Sealing of Metal and Plastic Tubes
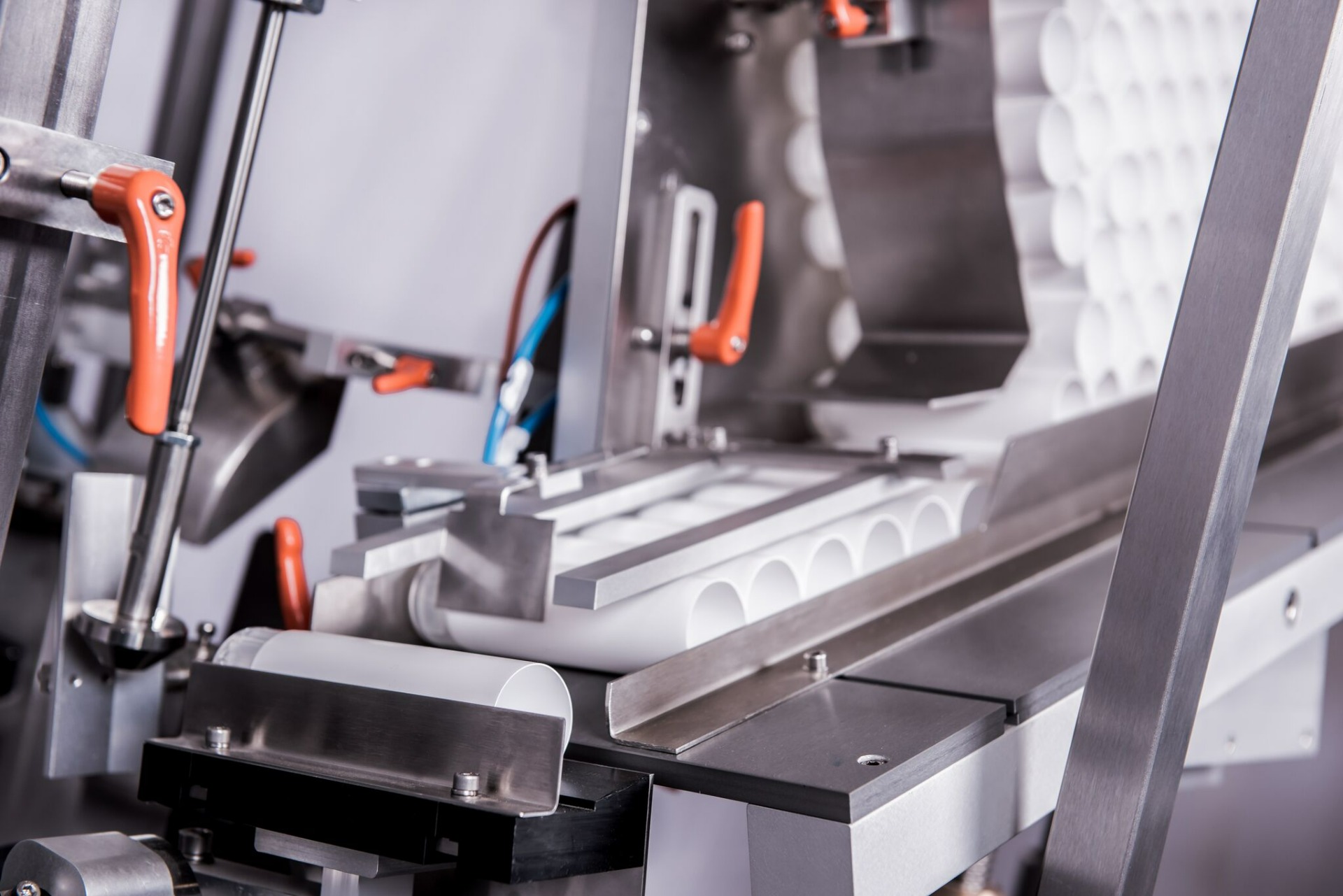
Key Features:
Machine frame with adjustable height legs.
Tube magazine equipped with automatic feeding.
Rotary table for seamless tube transfer between stations.
Tube orientation unit for precise alignment.
Product tank with a 35 L capacity and product level control.
Piston filling unit for accurate dosage.
Tube lift for bottom filling.
Pneumatically closed filling nozzle.
Hot air unit for seal heating.
Closing unit with embossing feature.
Trimming unit for a polished tube finish.
Automatic outfeed for filled tubes.
Control panel with a touch screen interface.
Safety guards for secure operation.
Overview:
The process begins with the manual loading of tubes into the tube magazine by the operator. These tubes are then automatically positioned into the tube holder, known as the "nest". A rotary table with nests shifts the tubes to the orientation position, aligning them based on a "black mark". The tubes then move to the filling unit, where the product is stored in a hopper and dosed using a volumetric cylinder. The filling volume can be adjusted as needed. The tube's top is heated by a hot air unit, followed by sealing. The tube top is then trimmed for a neat finish, and the completed tube is transferred to the outfeed conveyor.
Pharmline Robotic
Key Features:
4.5 meters long conveyor with adjustable guiderails (pharma execution).
Strong frame covered by AISI 304 stainless steel panels with a top covering gutter. The frame is placed on adjustable anti-vibration legs.
Mechanical main machine drive with variable speed, located inside the frame.
Star wheel operates with intermittent motion and is designed to handle the base size of bottles. It can be easily disassembled for quick format set changes.
Control of the presence of the bottle in the star wheel; if a bottle is missing, the machine stops.
4 precise peristaltic pump filling units. The dose is continuously and easily adjustable. Parts in contact with the product are FDA attested.
Nozzle holder with 4 into-neck non-drip filling nozzles.
A cam movement commands the diving nozzles' entry into the container neck.
De-capping and capping are performed using 2 Scara robots.
Siemens PLC controller enables control over various machine functions.
Overview:
The process starts when a closed bottle arrives at the machine via the infeed conveyor. The closed bottle is then guided onto the star wheel, a crucial component of the machine's operation.
The first robotic arm activates at this stage, responsible for opening the bottle. Once opened, the robot positions the cap on the star wheel, strategically located near the bottle. This cap can be placed on a special rod or slotted into a format part designed for this purpose.
Next, the open bottle moves to the filling stage, facilitated by the star wheel's indexing motion, ensuring precise positioning. Our system's filling process uses four peristaltic pumps, with each filling one quarter of the bottle's volume.
After filling, the second robotic arm retrieves the cap and securely closes the bottle. The closure uses a specifically calibrated torque level, ensuring the bottle is sealed to the required standard.
Once capped, the filled and closed bottle is directed out of the machine via the outfeed conveyor, completing the process.
Significantly, the entire operation is adjustable through the Human-Machine Interface (HMI), including recipe adjustments, filling processes, capping procedures, and more.
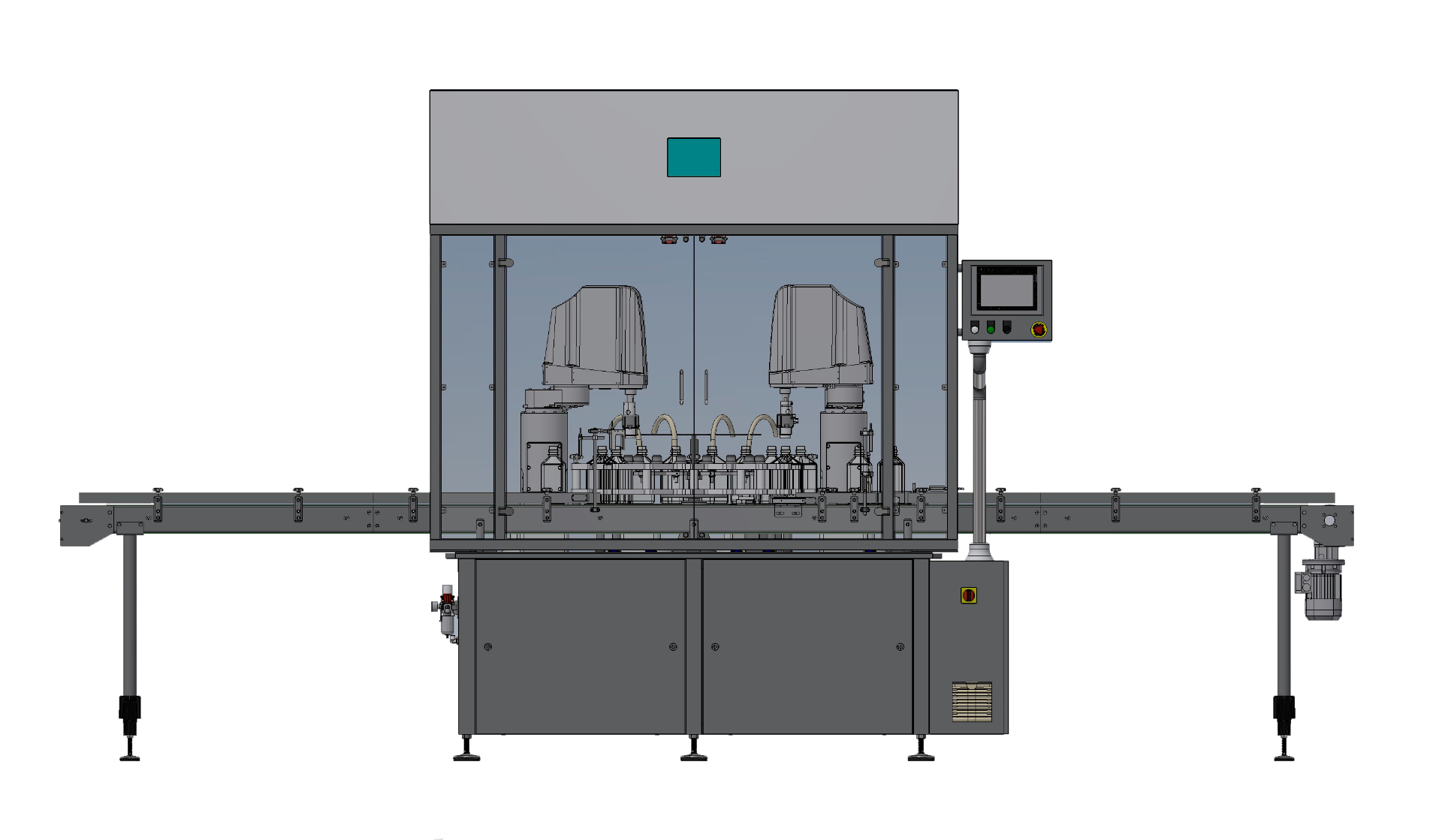